The Magic of Gear Trains: How They Help Watchmakers Harness Power and Precision
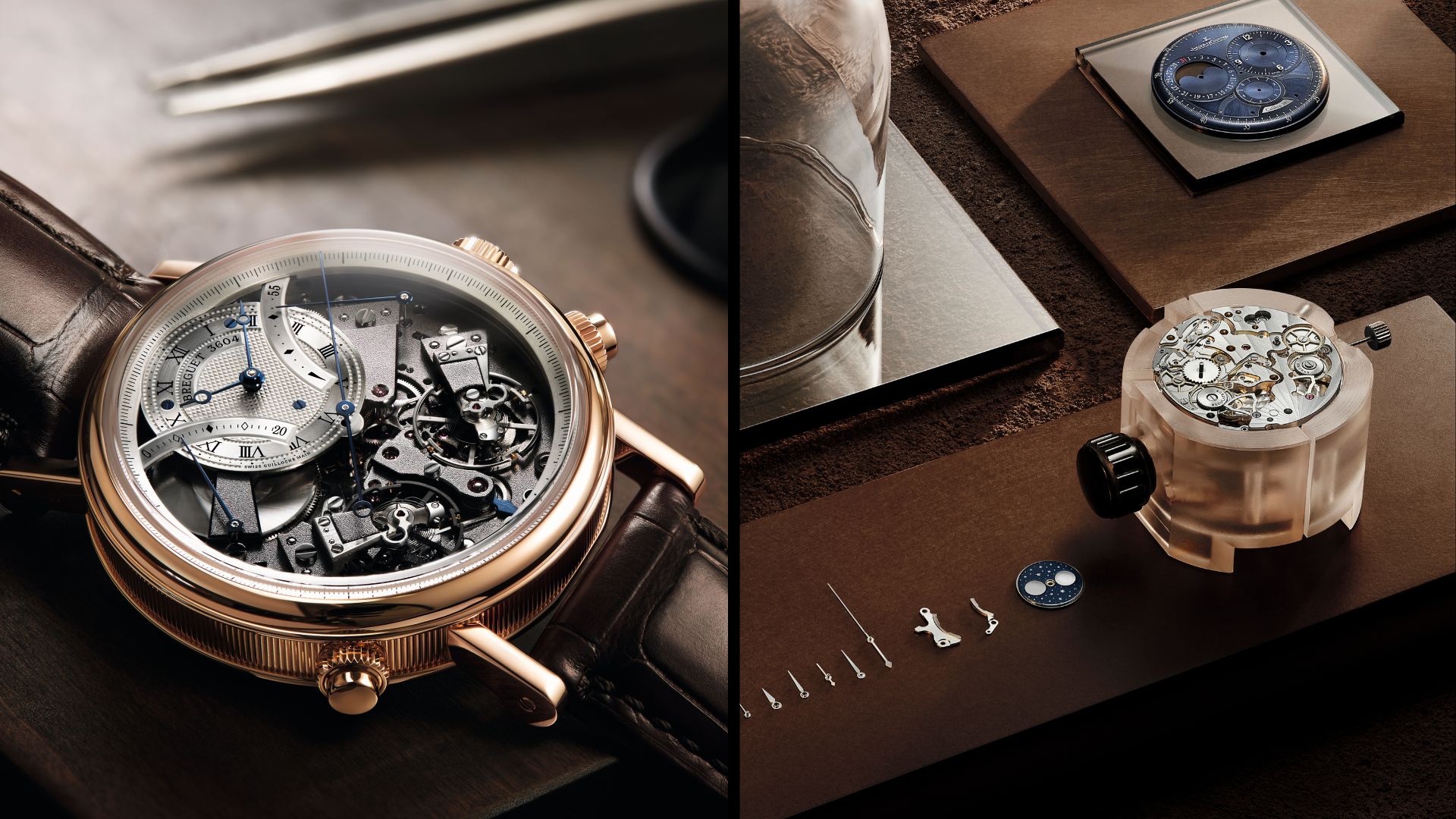
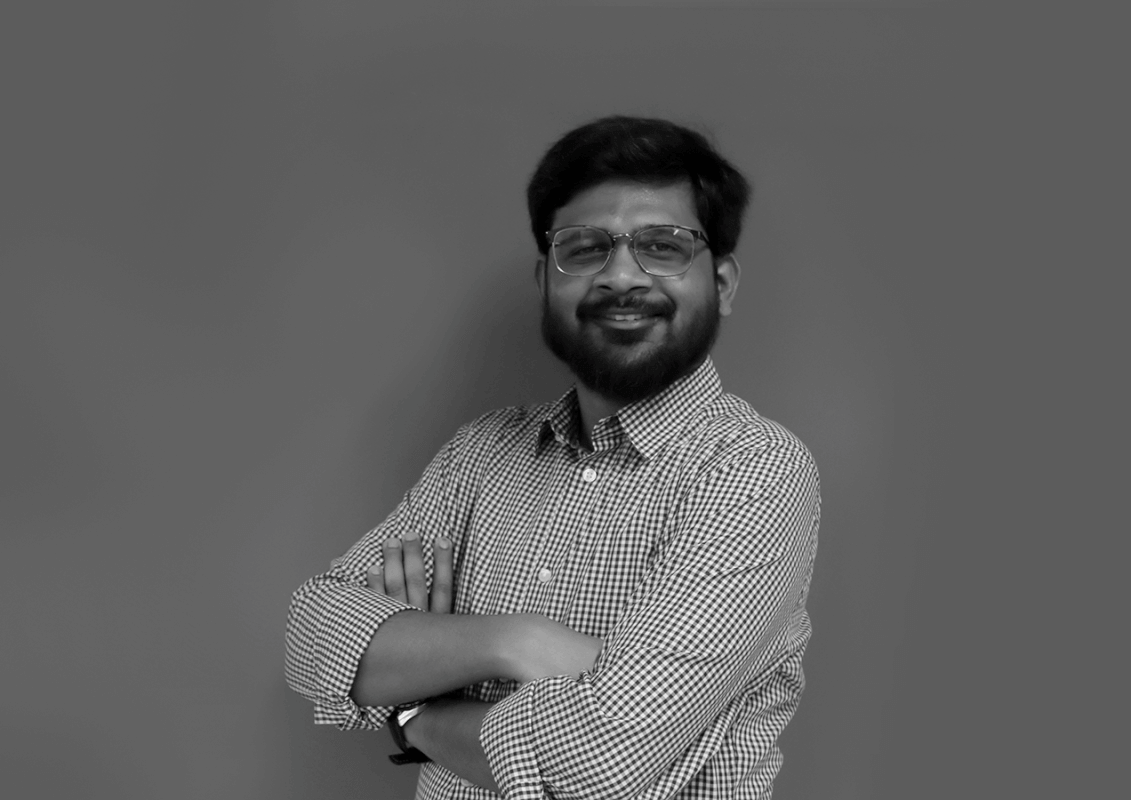
An essential component of mechanical timepieces, gear trains act as a complicated network that distributes energy from the mainspring of a watch to the escapement while controlling the movement of the timepiece’s hands. This series of interconnecting gears and pinions is built for precision and efficiency.
A gear train not only converts the mainspring barrel's high-speed revolution to the slower, controlled motion required for timekeeping, but it also makes it easier to divide time into hours, minutes, and seconds. Showing off a delicate balance between engineering and creativity, gear trains demonstrate watchmakers' inventiveness as even the tiniest of flaws in these components can impact a watch's accuracy and durability.
Significance in Horological History
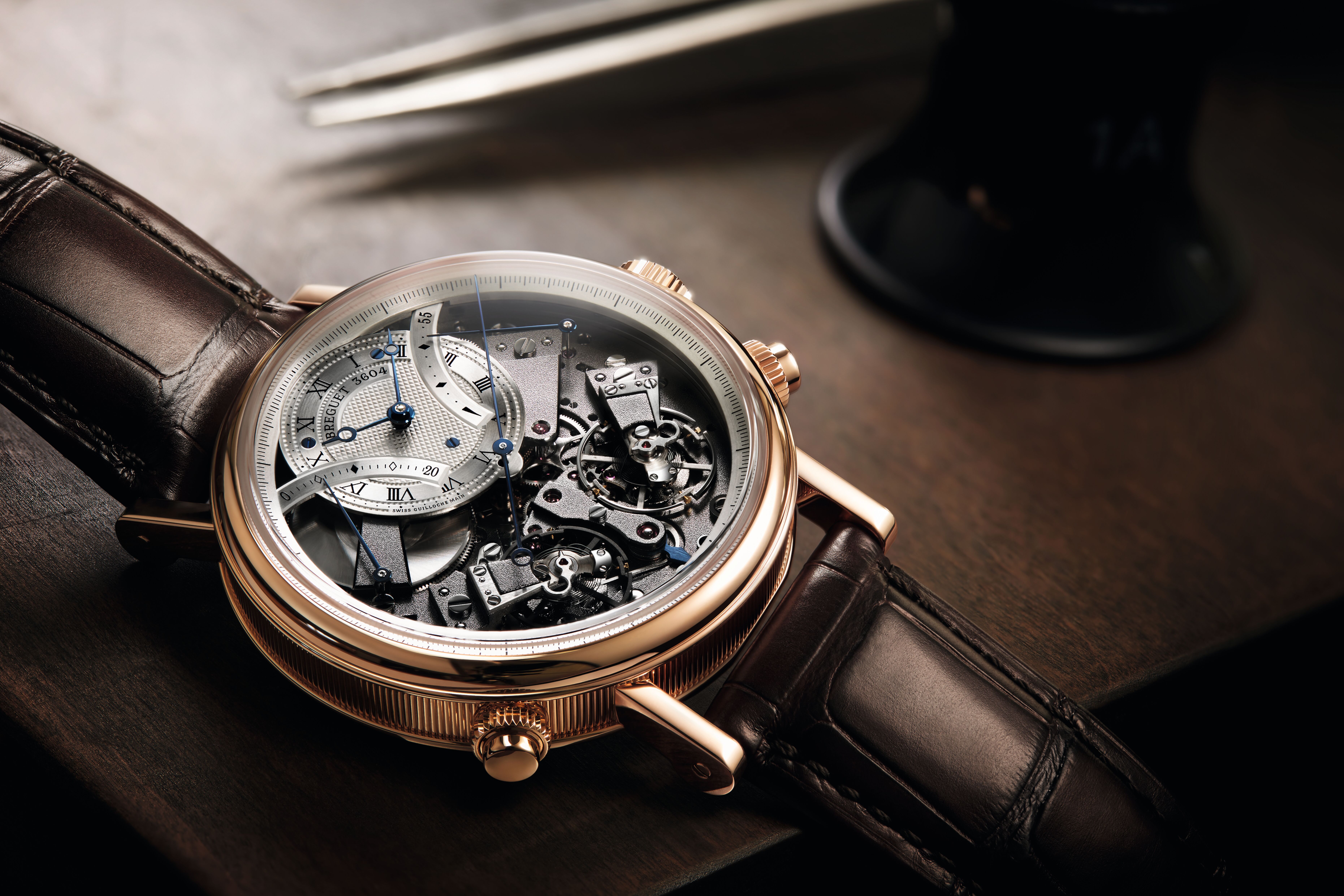
Gear trains are a defining feature of horological history, playing an important part in the evolution of timekeeping systems. These sophisticated sets of interlocking gears allow for exact regulation and transfer of energy from the mainspring to the escapement, ensuring accurate timekeeping. Since gear trains help divide time into hours, minutes, and seconds, they are the horological breakthrough that has transformed how people organise their lives.
Over the years, watchmakers have improved upon gear train designs to reduce friction and increase efficiency, resulting, first, in the development of tiny pocket timepieces and, later, wristwatches. Their value extends beyond practicality as the aesthetic arrangement of gears demonstrates the artistry and skill of watchmakers.
The Purpose
.jpeg)
Essentially, a gear train comprises a system of wheels and pinions that minimise the mainspring's high torque while raising its rotational speed to power a watch's hands. This exact method ensures consistent energy transfer, allowing the escapement to function properly, controlling the release of energy at defined intervals. Furthermore, a gear train is designed to let the hour, minute, and second hands move at their appropriate rates, ensuring that a watch displays time accurately and consistently.
A gear train typically consists of four wheels. The centre wheel is the first one and it is powered by the barrel; it is usually found in the centre of the action and rotates once an hour. The second wheel comes next. The third wheel follows the second wheel and revolves once each minute. Following the third wheel comes the escape wheel.
Materials and Craftsmanship
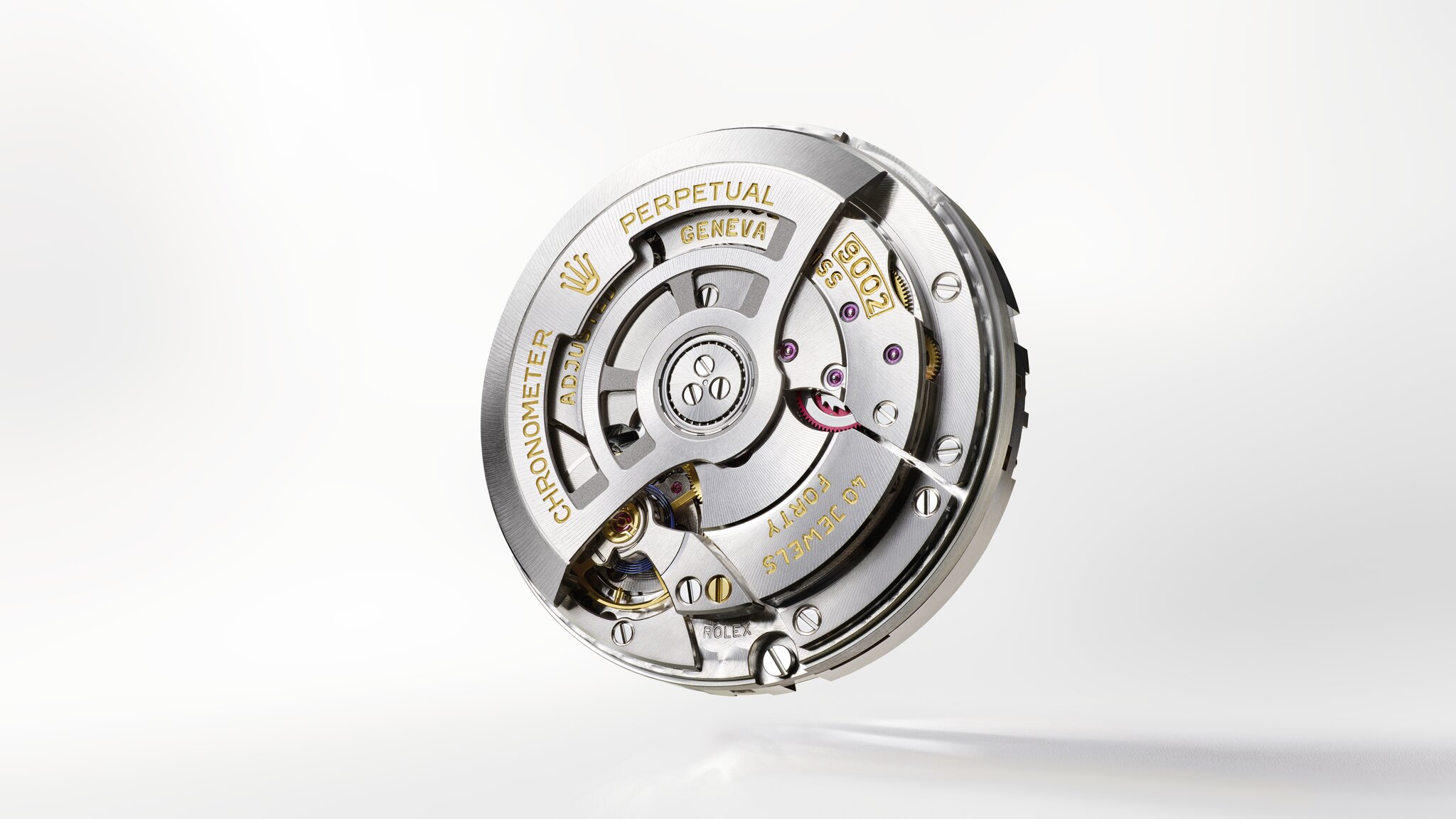
The materials that are used to build gear trains can considerably influence their efficiency and longevity. Metals, polymers, and composites are common materials for gears; they are chosen based on the application's strength, wear resistance, and cost-effectiveness. Steel, frequently alloyed with carbon or chromium, is a popular material for heavy-duty gears due to its outstanding strength and ability to tolerate high torque.
Brass and bronze are also commonly used in moderate-load applications due to their corrosion resistance and self-lubricating qualities. Aluminium is preferred in lightweight situations where precision is required, although it is less durable under large loads. Plastics like nylon and acetal are becoming increasingly popular for low-power, noiseless operations, thereby providing lightweight and cost-effective alternatives.
Innovations in Gear Train Design
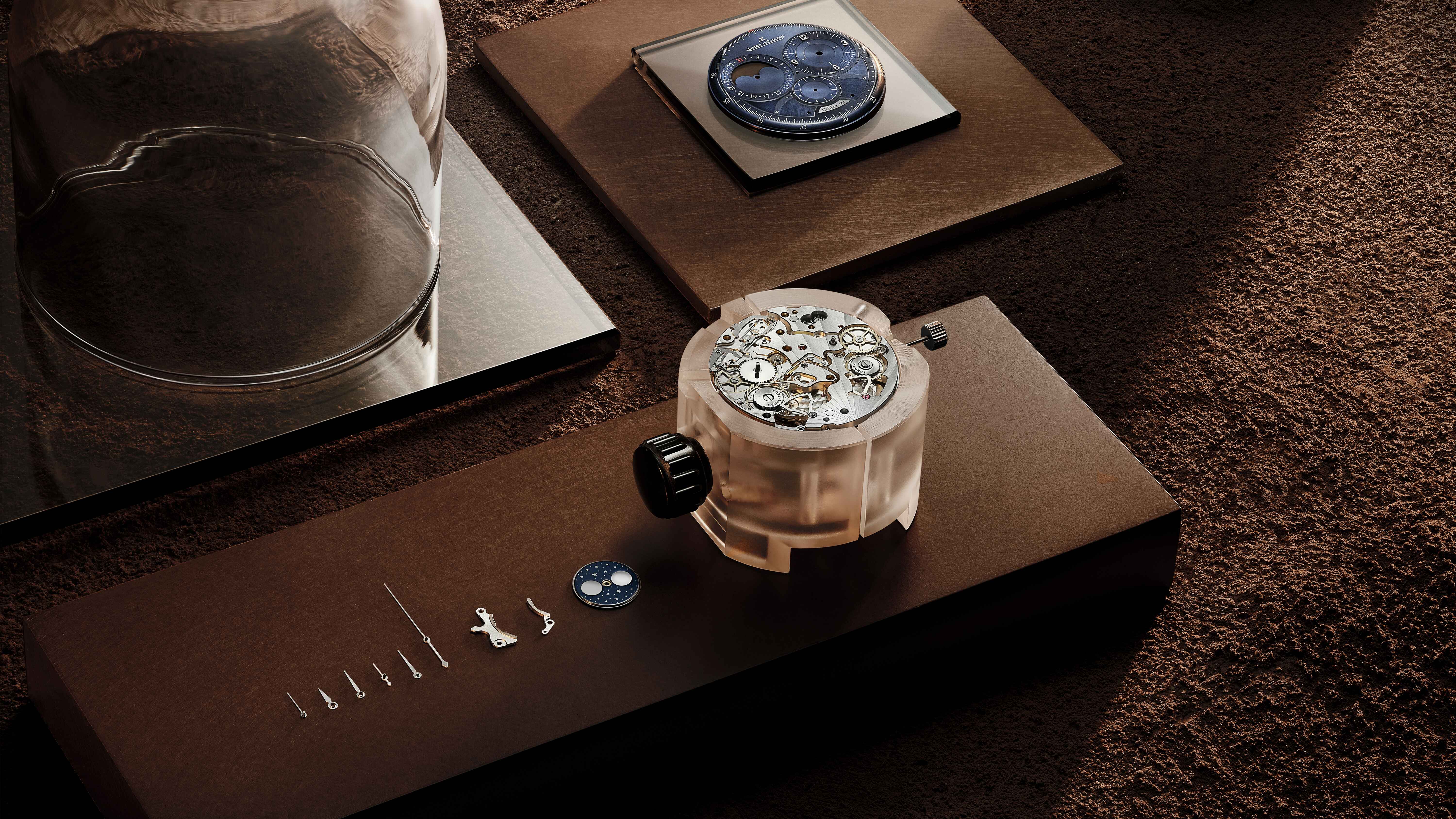
Innovations in gear train design have transformed the efficiency and precision of mechanical systems across multiple sectors. Modern advances aim to improve power transmission, reduce friction, and increase longevity. Use of materials such as titanium and ceramic has resulted in lighter and stronger gears while advances in manufacturing processes like 3D printing and CNC machining have allowed for the creation of complicated and very precise gear profiles.
Furthermore, computer modelling and AI-powered simulations enable engineers to optimise gear ratios and combinations for specific applications, ranging from high-performance clocks to industrial machinery. These advancements not only improve performance but also extend the lifespan of gear systems, making them more environmentally friendly and cost-effective.